LED UV-kikeményítés
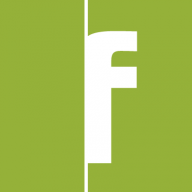
Az UV-lakkok kikeményítéséhez 2004-ben jelentek meg a piacon a LED UV fényforrások alkalmazásának új technológiáján alapuló első gépegységek (kisebb 3D tárgyakhoz). A technológia sík alkatrészeken történő első alkalmazásának laboratóriumi körülmények közötti tesztelésére négy évvel később került sor. A fejlesztés kezdetén bizonyos "nehézségek" léptek fel. A nagy hullámhosszú (395 nm) UV-sugárzás lehetővé tette a jó mélységi kikeményedés elérését, de gondok adódtak az UV-lakkok felületi kikeményedésénél is. A világítódiódák (LED) ebben az időben még nem rendelkeztek megfelelő teljesítménnyel és hatásfokkal. Ezért a LED UV fényforrást a lehető legkisebb távolságra kellett a munkadarab felületéhez közelíteni (3–5 mm), és biztosítani kellett az inert (oxigénmentes) környezetet. Ugyanis a levegőben lévő oxigén azokon a hullámhosszokon, melyeken a LED UV lámpák működnek, csökkentette az UV-sugarak hatékonyságát. Az inert környezetet a fényforrás és az alkatrész felülete közé történő nitrogénbetáplálással sikerült elérni.
Ezek a tények (a fényforrás és a munkadarab felülete közötti rendkívül kis távolság, valamint az inert környezet szükségessége) akadályozták a technológia gyakorlatban történő tényleges alkalmazását. Azóta azonban a technológiai fejlődés jelentősen előrehaladt. A LED teljesítménye az eredeti 1 W/cm2-ről 8–16 W/cm2-re nőtt. Néhány lépés egyszerűsödött, így például a kis távolságra és az inert környezetre vonatkozó elvárás teljesen megszűnt. Megváltozott a LED-mátrixhoz való csatlakozó érintkezések hűtési módja is. Eddig vízkörrel történt a fényforrások hűtése, ami a berendezés magasabb energiaszükségletét vonta maga után. A LED-modulok új generációjának hűtése már levegővel történik. Megjelentek a piacon a speciálisan ehhez a technológiához kifejlesztett új UV felületkezelő anyagok is. Az első tényleges ilyen típusú (Bürkle gyártású) gépsor a Cseh Köztársaság és a Szlovák Köztársaság területén belül 2012-ben Humpolecen, a fehér MDF-alkatrészeket gyártó BJS Czech vállalatnál került telepítésre és üzembe helyezésre.
A humpoleci BJC Czech gyárban két LED kikeményítő zóna található a felületkezelő gépsoron. A gépsor sík MDF bútoralkatrészeken pigmentált felület kialakítására szolgál.
SLM FÉNYFORRÁS
A szokványos felületkikészítési gépsorok kikeményítő egységeiben UV-kikeményítéshez fényforrásként hagyományos higany vagy gallium fénycsöveket használtak, melyek típustól függően gázzal vagy gőzkeverékkel töltött üvegcsövek. A fénysugarak egy irányba irányítását parabola reflektor biztosította. A modern LED UV kikeményítő egységek SLM-technológia elvén alapuló fényforrásokkal, UV világítódiódákkal (LED UV) vannak ellátva. Az SLM azaz Semiconductor Light Matrix (félvezetős világító mátrix) az UV-diódák sűrű mezejét mikrooptikai, úgynevezett MOEMS nyalábokkal (mikro-opto-elektro-mechanikus rendszer) kombinálja. Az optika felfogja a diódák által széles szögtartományban sugárzott fénysugarakat és a munkafelületre irányítja azokat, így fokozva a sugárzásuk erősségét. A világítótest felületén több ezer dióda van sűrű raszterbe rendezve. Ennek az elrendezésnek az eredménye a 100% szárazanyag-tartalmú, valamint a vízzel hígítható UV felületkezelő anyagok kikeményedését lehetővé tevő, nagyon intenzív UV-fény rendszer.
A LED UV lakk kikeményítésének kulcsfontosságú elemei a nagy hatásfokú LED-lámpák. Az alacsony hőmérsékletnek köszönhetően a fényforrás a kikeményítendő felület közvetlen közelébe helyezhető.
KIVÁLÓ HATÁSFOK – ALACSONY HŐKIBOCSÁTÁS
A LED-fényforrások fő előnyei közé általában a kiváló fényteljesítmény melletti alacsony energiafogyasztás és kismértékű felmelegedés tartozik. Míg a hagyományos higany (Hg) UVlámpák energiafogyasztásának 65–70%-a hővé alakul át és a lámpák felületi hőmérséklete 600–900 °C körül mozog (a kikeményített munkadarabok felületi hőmérséklete 50–80 °C), a LED UV fényforrások ilyen vonatkozásban csaknem 100% hatásfokúak. Az SLM világítótestek felületi hőmérséklete 40–50 °C körüli, és a kikeményített felület fölötti szokásos 10–15 mm távolság esetén a munkadarab felületi hőmérséklete legfeljebb 25–35 °C. Ez főleg a hőre különösen érzékeny anyagok felületkezelése esetén fontos tényező. Így elkerülhető a nemkívánatos hibák (például foltok, gyantakicsapódás erdeifenyő és más hasonló fafajok esetében, ragasztók és ABS-élek hőhatás által kiváltott lágyulása, fekete elszíneződés stb.) keletkezésének veszélye.
ALACSONY ENERGIAFOGYASZTÁS
A LED UV fényforrások kiváló hatásfokuknak köszönhetően sokkal kisebb intenzitással világíthatnak, mint a hagyományos UV-lámpák. Míg a közepes nyomású higanygőzlámpák energiafogyasztása kb. 15 kW, az azonos hatású ipari LED UV egységeké csak 7 kW körül mozog. A hagyományos fénycsövek teljes hatásfokra történő felmelegedéséhez és a teljes teljesítmény eléréséhez bizonyos idő szükséges. Azonban a LED-diódáknak jelentősen rövidebb a kapcsolási idejük (0,5 sec), így gyakorlatilag bekapcsolás után azonnal világítanak. Ennek megfelelően képesek rövidebb intervallumokban dolgozni, és ki lehet kapcsolni őket a munkadarabok gépsorra helyezése miatt szükséges rövidebb állásidőkre. A legmodernebb gépsorok mindezeken felül szkennerekkel vannak ellátva, melyek érzékelik a munkadarab körvonalát és annak megfelelően csak a világítótest meghatározott szakaszai kapcsolnak be, úgy, hogy csak a kikeményítendő felület legyen megvilágítva.
JOBB MUNKAKÖRNYEZET
A hagyományos közepes nyomású higanylámpák környezetvédelmi (veszélyes hulladékként kell ártalmatlanítani), valamint higiéniai és munkahelyi egészségvédelmi szempontból is veszélyt jelentenek. A legnagyobb kockázatot a higanygőz lehetséges belélegzése jelenti a törött lámpa kezelése (pl. lámpacsere) során vagy üzemeltetés közben. További kockázati tényező az ózon, mely légzési problémákat, sőt tüdőkárosodást is okozhat. A higany- és galliumlámpák az UV-fényt széles hullámhossz-tartományban sugározzák. A rövidebb hullámhosszú (180–220 nm) fény oxigén jelenlétében ózont hoz létre, melyet el kell távolítani a munkaterületről. A LED UV fényforrás a monokróm UVsugarakat olyan tartományban sugározza, melyben ózon nem keletkezik (kb. 395 nm). A LED UV források élettartama közel állandó teljesítmény mellett rendkívül hosszú. Teljesítményük a higanygőzlámpákkal ellentétben idővel nem változik, ezért nincs szükség folyamatos ellenőrzésükre és bemérésükre. A hagyományos higanygőz- és galliumlámpák üzemideje típustól függően 1–3 ezer óra. A LED UV források gyakorlatilag közel 15 ezer óra üzemidőt tesznek lehetővé.
TAPASZTALAT ÉS SZAKÉRTELEM
A Sherwin-Williams cégcsoport hosszú ideje kutatja és fejleszti A LED UV lakk kikeményítésének kulcsfontosságú elemei a nagy hatásfokú LED-lámpák. Az alacsony hőmérsékletnek köszönhetően a fényforrás a kikeményítendő felület közvetlen közelébe helyezhető. a LED-kikeményítéshez alkalmas anyagokat. A Sherwin-Williams számtalan kísérletet végzett különböző fafajokon és faalapú anyagokon, míg eljutott ahhoz a ponthoz, hogy megoszthatja a LED kikeményítési technológia minden előnyét ügyfeleivel. A LED-technológia a fa csaknem minden típusú – úgy átlátszó, mint színes – felületkezelésére alkalmas. A Sherwin-Williams cégcsoport ennek az új kikeményítési technológiának a bevezetésével segíti ügyfeleit a hagyományos UV-technológiáról az új LEDtechnológiára való áttérésben. A Sherwin-Williams cégcsoport szakemberei segítséget tudnak nyújtani a gyártósor átalakításában, tervezésében, tesztelésében és a gyártás beindításában is. A Sherwin-Williams cégcsoport LED-kikeményítési technológiája a maga nemében az első olyan technológia, mely ügyfeleinek a legmodernebb, energiahatékony és egyben környezetkímélő technológia alkalmazásával egyedülálló felületkezelést tesz lehetővé.