Beszélgessünk a kompresszorokról
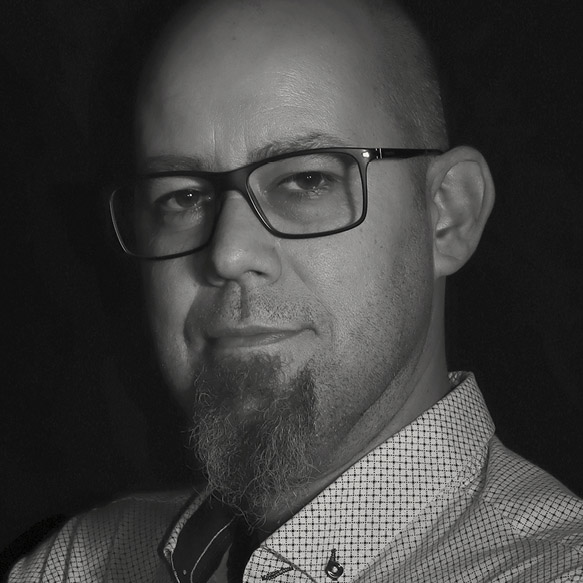
Minden műhely életében eljön az az idő, hogy szükség lesz pneumatikára. Ezt három dolog szokta indukálni: valamilyen új gépünkhöz segédenergia szükségeltetik, szeretnénk levegős szerszámokat üzemeltetni, s mert kell. Ez utóbbi kicsit talán erős és indokolatlan igénynek tűnik, de nem egy esetben kértek tőlem tanácsot kompresszorvásárlással kapcsolatban. Amikor megkérdeztem, hogy milyen célra, akkor a válasz az volt, „hogy legyen”. Ezzel annyira megy az ember fia, mint életlen késsel nyél nélkül. Merthogy a sűrített levegő előállítása és felhasználása a legköltségesebb művelet, ami egy műhely életében lehet a raktárkészlet mellett (bár ez utóbbival az utóbbi időkben lehet és kell is vitatkozni). Jelen cikkem igyekszik elnavigálni az olvasót a számok és a technológia világában, hogy el tudjuk dönteni, milyen kompresszorra, vagy komplett rendszerre tegyük félre a pénzünket.
A mai napig alig találkozni olyan asztalos-, vagy faipari műhellyel, ahol ne látnánk locsolócsőre emlékeztető, „sziszegő” végű eszközöket. A sűrített levegős rendszerek jelenléte a műhelyben egyszerre áldás és egyszerre gyötrelem is. Áldás, hiszen rengeteg gép és eszköz üzemeltethető róla, illetve takarítóeszközként is kiválóan funkcionál. Ez utóbbival kapcsolatban azért vannak félreértések, ami a munkaruha ilyen formán történő tisztítását illeti. (A por, forgács egy jó része tényleg eltűnik, de egy másik hányada csak mélyebbre kerül a szövetben. Ez egyébként bőrirritációt okozhat.). Sok gépnek szüksége van segédenergiára, és ez a legkönnyebben a sűrített levegő rejtett energiáját jelenti. Pneumatikus munkahengerek által szolgáltatott leszorítók, motorok, anyagtovábbítók szinte minden iparágban fellelhetőek. Az ok egyszerű és sokan nem is gondolnak rá, mert adott a rendszer, a technológia. Egy hidraulikus rendszerrel ellentétben, az energiát szolgáltató közeget elegendő csupán a felhasználási területre juttatni. Az „elhasznált” energiát, jelen esetben az expandált, kitágult levegőt büntetlenül juttathatjuk a légtérbe. A csőhálózat kiépítése is viszonylag egyszerű feladat, ha az ökölszabályokat betartjuk. De akkor miért írom, hogy gyötrelem?
A mai napig alig találkozni olyan asztalos-, vagy faipari műhellyel, ahol ne látnánk locsolócsőre emlékeztető, „sziszegő” végű eszközöket. A sűrített levegős rendszerek jelenléte a műhelyben egyszerre áldás és egyszerre gyötrelem is.
A GYÖTRELEM OKAI
Az első probléma, hogy a sűrített levegő előállítása költséges mutatvány. Szükségünk van egy jó hatásfokú légsűrítőre, ami jellemzően valamilyen dugattyús mechanizmus (szó lesz a nem dugattyús alternatívákról is), amit egy villanymotorral hajtunk meg (ez robbanómotor is lehet). Ezután valamilyen csőhálózaton juttatjuk el a felhasználási területre, és ott jellemzően valamilyen egyenes vonalú, vagy forgó mozgássá alakítja az adott fogyasztó (van egyéb felhasználás is). Természetesen egy felületkezelési eljárás esetében más lesz a szituáció, de a lényeg ott is az, hogy a fogyasztó milyen hatásfokkal és milyen fogyasztási értékekkel szerepel a rendszerben. Az így összeadódó veszteségek rosszabb esetben közelíthetik egy dízelmotorét. Ha ez nem lenne elég, akkor ott van az, hogy ami elodázható, azt el is odázzuk. Ez pedig nem más, mint a légsűrítő és a közvetlenül vele szoros kapcsolatban álló légtartály karbantartása. A jó és hatékony sűrítettlevegő-ellátás első védvonala ez. Mivel az egész rendszer tele van gyenge pontokkal, a drasztikus hatásfokcsökkenés megjelenésekor a légsűrítő sok esetben költségtöbblettel javítható csak.
Dugattyús kompresszor működése.
De akkor miért olyan elterjedt? Mert relatíve könnyűek az eszközök, rugalmasan bővíthető a rendszer és vannak olyan technológiák, amelyeket direkt erre fejlesztenek a mai napig. Ilyen a szórástechnika is, ami engem is elindított a múlt század végén a kompresszorok építésének útján. Ez egy kalandos, sok tapasztalatot eredményező többéves projekt volt. A végeredmény azonban az lett, hogy kell egy megbízható, jó minőségű gyári kompresszor.
SZEGÉNY EMBEREK KOMPRESSZORA
Nos, a recept egyszerű. Végy egy légsűrítőt. Ezt jellemzően egy tehergépjárműből építik be. Olcsó, egyszerű, és az alkatrész-utánpótlás biztosított. AVIA, IFA, KAMAZ, RÁBA/IKARUS stb. Az orosz technika hátránya, hogy fogaskerekes a kihajtása, ezért ez bonyolítja az építést, ebből kifolyólag ezt általában nem alkalmazzuk. Az AVIA léghozama kicsi. Az IFA kompresszora is elmarad a várttól, ezért az úgynevezett CSONKA kompresszor az egyik legjobb választás, de ennek vízhűtésre van szüksége, valamint a kompresszor kenésével is kell kicsit bütykölni. Érdekes, de a mai napig gyártják, igaz, nem Győrben, mint rég.
Egy 100 m³/perc teljesítményű, 15 baros csavarkompresszor (felvetődik a kérdés, hogy milyen megmunkálógép kellett a precíz gyártáshoz).
Ezek után már „csak” egy nyomásálló tartályra van szükségünk. Többnyire itt bukik el a dolog és válik veszélyessé. Már pár bar nyomású tartály is képes lebontani a fél műhelyt, hát még, ha 10 barra töltjük és elhagyjuk a biztonsági szelepet, s a hegesztéseket is magunk végezzük. Akkor már inkább egy minősített tartályt igyekezzünk beszerezni, bár ha az használt, akkor van kockázat. Senkit sem szeretnék házi kompresszorkészítésre bátorítani, mert bár egyszerűnek tűnik, óriási veszélyei lehetnek.
MEKKORA LEGYEN A KOMPRESSZOR?
A kérdést több oldalról kell megközelíteni, de azt is mondhatjuk, hogy a kérdés eleve rossz! Van a kompresszor, ami a légsűrítő, és van a tartály, ahol tároljuk a légsűrítő által előállított sűrített levegőt (izgalmas, hogy van olyan légsűrítő rendszer, ahol nem szükséges légtartály, mivel a csőhálózatot használja erre a célra).
A két legnagyobb félreértésre okot adó adat a légtartály térfogata és a légsűrítővel előállítható nyomás. Van ugyan összefüggés, de a két értékből nem következtethetünk a rendszer „jóságára”. Nézzünk egy példát. Adott egy 100 literes tartály, aminek elvileg elegendőnek kellene lennie egy normál pár fős műhely ellátására. És van egy hozzá kapcsolt légsűrítőnk, ami 150 l/perces légtermelést biztosít 8 bar maximális nyomással a szállított oldalon. Kérdés, ez így jó-e? A válasz: nem. Mert már egyetlen pneumatikus gépet sem fog tudni tartósan kiszolgálni, vagyis a kompresszor folyamatosan fog üzemelni, hogy a tartályt feltöltse. Ez vegyes használatú fogyasztók mellett tovább romlik és szüneteket kell beiktatni a munkavégzésben, holott a tartály nagy! Valóban, de ez olyan, mintha egy medencét szeretnénk merülőforralóval felmelegíteni. Életszerű példa okán írom, hogy a népszerű 24 literes kompresszor „kategória” megvásárlása után a tartálybővítés, vagy csere nem, vagy csak átmeneti megoldást fog nyújtani az időszakos téli-nyári autókerekek cseréjére, a légkulcs meghajtására. Festékszórásra, csiszolásra, fúrásra már nem lesz alkalmas, mert az üzemi nyomás (tartály 8 bar, nyomásszabályzás után a rendszer nyomása 6 bar), s a léghozam hamar kimeríti a puffert. De akkor mire alkalmas egy 8 bar nyomást produkáló 110 liter/perc szívóoldali teljesítményű kompresszor? Szegbelövők, gumiabroncsfújók, pneumatikus munkahengerek és egyéb kis üzemciklusú eszközök működtetésére. Ugyanis a ciklus és a fogyasztás is fontos, de erről később.
Mielőtt teljesen elvesztenénk a fonalat, tisztázzuk a tartály feladatát! A megtermelt levegőt puffertartályként (azaz tartalék) használva, kiküszöbölhető az alkalmanként hirtelen fellépő levegőigény nagyobb nyomásesés nélküli biztosítása. Ez olyan felhasználási területeken hasznos, ahol egyszerre sok levegő szükséges (általában több, mint a kompresszor szállított levegő percenkénti mennyisége). Ahol a levegőigény meghaladja a kompresszor termelési határértékét, a felhasználási műveletek hosszabb ideig folytathatóak, így időt nyerhetünk vele. De a tartály nem lehet aránytalanul nagy, mert akkor annak feltöltése aránytalanul sok időt vesz igénybe.
Jellemzően a ki- és bekapcsolási érték különbsége 2 bar. Azonban, ha egy nagyobb fogyasztású eszközt használunk, akkor mire bekapcsol a kompresszor, már rég az üzemi nyomás alá kerülhet a rendszer. Ezt a tartály térfogatával sem tudjuk kompenzálni. 6 bar az üzemi nyomás.
A sűrítettlevegő-tartály beépítése nem jelent megoldást a kompresszor kapacitását meghaladó folyamatos igény kielégítésére. A tartalék levegő közvetve elősegíti a start/stop rendszerű készülékek visszahűlését, valamint a start/ stop – terhelt/üresjárati készülékek ritkább szabályozását, kímélését. Így a megfelelő levegőellátás kalibrálásához nem a puffer mérete, hanem az elvétel és a kompresszor kapacitása az elsődleges szempont. A megfelelő tartályméret kiválasztásánál javasolt két szempont figyelembevétele. Az egyik alapelv, hogy a szállítottlevegő-mennyiség 0,4 szorzatával kapjuk meg az ideális méretet. Fordulatszám-szabályzású készülék esetén ez csökkenhet, hiszen a szabályzás miatt kisebb puffertérfogat is elegendő. A nagy tartály nem biztosítja a folyamatos munkavégzést abban az esetben, ha a kompresszor által szállított levegő kevesebb, mint a felhasznált mennyiség. Egy közepes teljesítményű szállítottlevegő-mennyiség ~650 liter/perc@11 bar. A szorzást követően 260 literes tartályt kell kapnunk az adott légsűrítőhöz.
A SZÁLLÍTOTT LEVEGŐ MENNYISÉGE ÉS A NYOMÁS KAPCSOLATA
A kompresszorok (légsűrítő+légtartály) kiválasztásakor az a ténylegesen szállított levegőmennyiség a mérvadó, ami a sűrítés után rendelkezésére áll, s ennek a men - nyiségnek valamivel nagyobbnak kell lennie, mint az egyes szerszámokon, gépeken, munkahengereken megadott fogyasztásainak összege. A dugattyús kompresszorok esetében szinte kizárólag csak a szívott teljesítményt (a lökettérfogat és a fordulatszám szorzata) adják meg, mivel ez egy egzakt érték. Ennek oka, hogy a nyomáson mért légszállítási értékeket számos tényező befolyásolja (pl. beszívott levegő hőmérséklete, páratartalma, nyomásszint, kompresszor kialakítása, állapota stb.).
Számunkra az a légszállítási men - nyiség a fontos. Amennyiben nem találunk tényleges légszállításra adatokat, akkor a szívott teljesítményből kiindulva, egyfokozatú kompresszorok esetében 60–70 százalék, kétfokozatú kompresszorok esetében 65–75 százalék szállított teljesítménnyel számolhatunk, a fent leírtak figyelembevételével. Itt is van egy kis csavar a dologban, mivel minél nagyobb a nyomás, ez az érték kisebb. Tehát 8 baron a szállított teljesítmény nagyobb, mint 10–11 baron. Ez utóbbi nyomásérték egyre gyakoribb. Viszont olcsóbb kompresszorok esetében a nyomáskapcsolót erre az értékre állítani egyenlő a kompresszor gyorsabb kopásával.
A nyomáson mért légszállítást saját magunk is meghatározhatjuk: ehhez meg kell mérni az időt, ami az alsó P1 (bekapcsolási) és a felső P2 (kikapcsolási) nyomás eléréséhez szükséges. Ezt egyébként hiszterézisnek is hívjuk. Jobb nyomáskapcsolókon ez az érték precízen beállítható. A tényleges légszállítás (közelítő érték) az alábbi képlettel számítható ki: Tartálytérfogat x (P2 – P1) x 60 / mért idő (s). Példa: 100 literes tartály 30 másodperc 8-ról 10 barra. 100 x (10-8) x60:30 = 400 l/min. A kompresszor tehát kb. 400 l/min légszállításra képes. Ezzel a módszerrel akár rendszeres (évenkénti) ellenőrzés is lehetséges.
A Danfoss KP 36 típusú nyomáskapcsolója. A hiszterézis állítása külön történik, és már majdnem labortechnikára is alkalmas.
HISZTERÉZIS
Jellemzően a ki- és bekapcsolási érték különbsége 2 bar. Azonban, ha egy nagyobb fogyasztású eszközt használunk, akkor mire bekapcsol a kompresszor, már rég az üzemi nyomás alá kerülhet a rendszer. Ezt a tartály térfogatával sem tudjuk kompenzálni. 6 bar az üzemi nyomás. A kompresszor 8 baron kapcsol ki és 6 baron be. A légfogyasztás folyamatos, és a kompresszor nem is tudja a fogyasztó levegőszükségletét fedezni, ezért a rendszer a fogyasztás megszűnéséig mínuszban marad. A helyzetet súlyosbítja, ha más fogyasztókat is bekapcsolunk. Ilyenkor két választás van. Az egyik, hogy a kompresszor kikapcsolási értékét növeljük, vele együtt a bekapcsolási küszöb is nő. Ezzel két anomália keletkezik. Az első, hogy a kompresszor élettartama csökkenhet. Ez ugyan nem biztos, de az igen, hogy a nyomásoldali légszállítás csökken, vagyis a tartály feltöltéséhez több időre van szükség.
A másik, hogy a hiszterézisen változtatunk. Azaz a nyomásérték plafonja marad, de a bekapcsolási értéket növeljük, 7–7,5 barra. Ezt sem tehetjük büntetlenül. A kompresszor gyakrabban fog bekapcsolni, s ha ez kezd majdhogynem folyamatossá válni, akkor szintén a kompresszor idő előtti tönkremenetelét jelentheti. 1–3 fős műhelyekben ez működhet, de figyelni kell. Sajnos nem minden nyomásszabályzó alkalmas a hiszterézis pontos beállítására, ezzel számoljunk.
Dugattyús kompresszorok esetében a dugattyú alternáló mozgása végzi a levegő sűrítését. Kenése olajos gépek esetében általában szóró olajozással történik, hűtéséről pedig ventilátor gondoskodik. A kereskedésekben kapható kompresszorokat szakaszos üzemet feltételezve tervezik és gyártják. Típustól, kialakítástól függően, a gyártó megadja az üzemidő- és a pihenőidő-ciklus arányát (S3/25, S3/50, S3/75). 5 vagy 10 perces ciklus esetében előírja az üzemidő és az állásidő százalékos arányát, a kompresszor elemeinek védelme érdekében. Folyamatos levegőigény esetén ez azt jelenti, hogy típustól függően akár többszörös mértékben kell fölé méretezni. Olcsóbb, vagy épített kompres - szorok problémás alkatrészei a következők: olcsó nyomáskapcsolók, szabályozóegységek, csatlakozók, visszacsapó- és biztonsági szelepek.
OLAJKENÉSES VAGY „SZÁRAZ” KOMPRESSZORT?
Az olajmentes kompresszorok által előállított levegője sem tiszta. A levegő minőségét a levegő utókezelése határozza meg. A barkács célú, olajmentes dugattyús kompresszorok esetében a kenési rendszer elhagyása az olcsóbb felépítést teszi lehetővé, s az élettartamuk jelentősen rövidebb a szakszerűen üzemeltetett olajos kompresszorokénál. Olajmentes kompresszor alkalmazását többnyire csak speciális felhasználási körülmények indokolhatják: extrém üzemeltelési körülmények, gázok utósűrítése, gyógyászati, vagy labortechnika.
CSAVARKOMPRESSZOROK
A csavarkompresszorok a rotációs kompresszorok csoportjába tartoznak. A csavarkompresszorokban két orsóformájú, egymásba kapcsolódó rotor található. A főrotor a felvett energia 85–90 százalékát alakítja át nyomás- és hőenergiává. A mellékrotor a szívó- és nyomóoldal közötti munkatér (rés) letömítéséről gondoskodik. A sűrítésnél a rotorok előrehaladó forgása zárja a levegő beömlő nyílását, és a levegő térfogatát csökkenti, növekvő nyomás mellett. Ezzel egyidejűleg olajat fecskendezünk a rendszerbe kenés, tömítés és hőelvezetés céljából. Sűrítési végnyomás: max. 13 bar. Működésükből adódóan a csavarkompresszorok folyamatos üzemelésre képesek, viszont megfelelő minőségű olajzárra van szükségük. Amennyiben a levegő-felhasználásból adódóan a kompresszor nem képes elérni az üzemi hőmérsékletet (keveset és ritkán üzemel), úgy kondenzvíz-kiválás történik az olajkörben, ami a gép károsodását okozhatja. Előnye, hogy nincs alternáló mozgás. Kicsit olyan a helyzet, mint a Wankel-motorok esetében. A kenésre nagy hangsúlyt kell helyezni. A karbantartási idők betartása fontos. Cserébe csendes és hatékony légsűrítőt kapunk, amely egy minimális méretű tartállyal üzemeltethető.
Forrás:
www.kompresszormester.hu
http://www.draspo.hu
Kapcsolódó dokumentum:
beszelgessunk-a-kompresszorokrol